轴承钢盘条冷镦套圈开裂原因分析及改进措施
2021-02-24肖训军
(南京钢铁有限公司)
(南京钢铁有限公司)
前言
某用户使用南钢18mm规格某批次轴承钢盘条GCr15-Y,中间经辊底式连续炉退火,连续退火炉为氮气保护真空锁气辊底式球化退火炉。
球化退火工艺流程为:来料检验→装框上进料台→进前真空室(抽空气充氮气)→由真空室进入预热区、升温区、保温区、快冷区、等温区、缓冷区、自由冷区(热装炉升温到795℃,保温7h,快速冷却到720℃,保温5h,以20℃/h冷却速度降至650℃出炉)→进入冷水仓→进后真空室→出料台。
退火料经过原料检验→酸洗→磷皂化→轻拉一道30丝→下料冷镦成毛坯套圈,肉眼可见套圈端面存在开裂现象,开裂比例在10%~15%之间,开裂位置不连续,裂缝位置沿盘条径向垂直于轧制延伸方向,如图1所示。
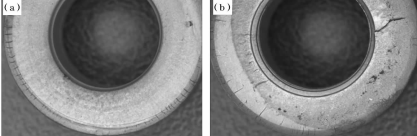
图一
用户反馈球化退火、拉丝、冷镦工艺正常,只有本批次轴承钢盘条冷镦套圈开裂比例超出10%,与原始盘条关系较大。
盘条生产工艺为:坯料抛丸、点磨处理→步进式加热炉加热(预热段700~750℃、加热一段930~960℃、加热二段1130~1160℃、均热段1200~1240℃,加热二段和均热段高温段时间60~100min。)→高压水除鳞→粗轧→中轧→预精轧→一区水冷→精轧→二区水冷→减定径→三区水冷→吐丝→斯泰尔摩风冷→集卷→精整→打捆→称重→入库。
1 开裂套圈样品分析
从开裂套圈样品中随机取4个样,其中2个套圈用作高、低倍检验和硬度分析,另外2个套圈用作碳化物不均匀性及断口检验、晶粒度分析。
1.1宏观检查
从套圈开裂样品中随机挑选1个,在体视显微镜下观察,套圈开裂宏观形貌如图2所示。
1 开裂套圈样品分析
从开裂套圈样品中随机取4个样,其中2个套圈用作高、低倍检验和硬度分析,另外2个套圈用作碳化物不均匀性及断口检验、晶粒度分析。
1.1宏观检查
从套圈开裂样品中随机挑选1个,在体视显微镜下观察,套圈开裂宏观形貌如图2所示。
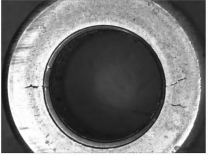
图二
1.2低倍检验
将其中一个套圈在热盐酸(浓度31%,温度70~80℃)中浸蚀8~10min后取出,宏观检查,发现套圈的正反两端面均存在多条裂纹正面如图3a所示,反面如图3b所示。
将其中一个套圈在热盐酸(浓度31%,温度70~80℃)中浸蚀8~10min后取出,宏观检查,发现套圈的正反两端面均存在多条裂纹正面如图3a所示,反面如图3b所示。
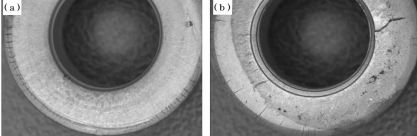
图三
将另一个套圈试样的一端面磨去2~3mm,并沿纵截面切除一部分,在热盐酸(浓度31%,温度70~80℃)中浸蚀8~10分钟后取出,按国标/GBT18254评定中心疏松和一般疏松均为1.0级,未见缩孔缺陷存在,形貌如图4所示。因此套圈端面开裂与原材料低倍组织无关。

图四
1.3高倍检验
1.3.1套圈裂纹退火态检验
在图2右侧端面两条裂纹处取样经打磨制备后,显微镜下观察纵截面,开裂的裂纹内及周围均未见夹杂物、氧化物存在,腐蚀后观察,裂纹两侧与基体显微组织一致,为铁素体基体上分布着球粒状珠光体,试样边缘与裂纹处均未见脱碳现象,如图5所示裂纹对面端面取样制备后观察,横截面上的裂纹两侧与基体显微组织一致,为铁素体基体上分布着球粒状珠光体,如图5所示。
1.3.1套圈裂纹退火态检验
在图2右侧端面两条裂纹处取样经打磨制备后,显微镜下观察纵截面,开裂的裂纹内及周围均未见夹杂物、氧化物存在,腐蚀后观察,裂纹两侧与基体显微组织一致,为铁素体基体上分布着球粒状珠光体,试样边缘与裂纹处均未见脱碳现象,如图5所示裂纹对面端面取样制备后观察,横截面上的裂纹两侧与基体显微组织一致,为铁素体基体上分布着球粒状珠光体,如图5所示。
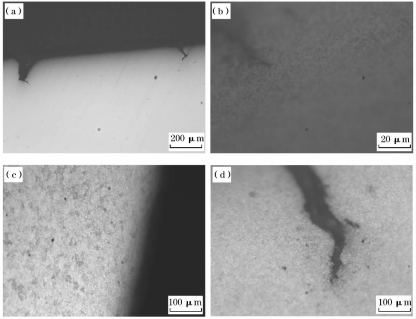
图五
1.3.2碳化物不均匀检验
将一套圈经淬回火处理后,在显微镜下检验纵截面碳化物不均匀性,发现带状、网状形貌如图6所示,按国标GB/T18254评定为带状级,网状1.5级,未见碳化物液析存在,满足国标要求。因此套圈端面开裂与原材料碳化物均匀性无关。
将一套圈经淬回火处理后,在显微镜下检验纵截面碳化物不均匀性,发现带状、网状形貌如图6所示,按国标GB/T18254评定为带状级,网状1.5级,未见碳化物液析存在,满足国标要求。因此套圈端面开裂与原材料碳化物均匀性无关。
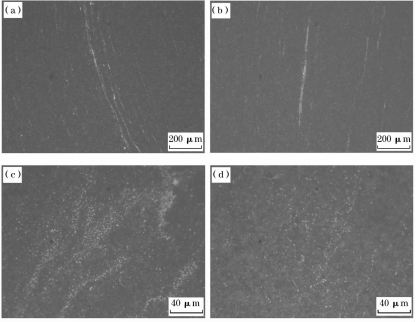
图六
1.4套圈布氏硬度检验
沿套圈圆环方向随机进行布氏硬度检测,硬度较为均匀,平均硬度为290.8HB,未发现明显的高点或低点,检测数据如表1所示。
沿套圈圆环方向随机进行布氏硬度检测,硬度较为均匀,平均硬度为290.8HB,未发现明显的高点或低点,检测数据如表1所示。

1.5套圈断口检验
一套圈经淬火处理后,一次击断,借助体视显微镜检验套圈纵截面断口组织,在宏观断口表面上有许多亮面,每个亮面都是一个晶粒的界面,断裂路径沿着不同位向的晶界延伸,为典型的沿晶脆性断裂,形貌如图7所示。
根据断裂能量消耗最小原理,裂纹的扩展路径总是沿着原子键合力最薄弱的表面延伸,在很大程度上取决于晶界面的状态和性质。晶界强度不一定最低,但如果金属存在着某些冶金因素使晶界弱化(例如钢坯出现过热或过烧),则金属将会发生沿晶脆性断裂。
一套圈经淬火处理后,一次击断,借助体视显微镜检验套圈纵截面断口组织,在宏观断口表面上有许多亮面,每个亮面都是一个晶粒的界面,断裂路径沿着不同位向的晶界延伸,为典型的沿晶脆性断裂,形貌如图7所示。
根据断裂能量消耗最小原理,裂纹的扩展路径总是沿着原子键合力最薄弱的表面延伸,在很大程度上取决于晶界面的状态和性质。晶界强度不一定最低,但如果金属存在着某些冶金因素使晶界弱化(例如钢坯出现过热或过烧),则金属将会发生沿晶脆性断裂。
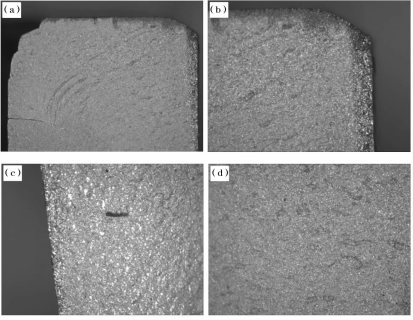
图7
1.6套圈奥氏体晶粒度检验
制备断口纵截面试样在显微镜下检验晶粒度,发现套圈外壁晶粒度明显比基体晶粒度要粗,形貌如图8所示。因此推测断口试样与原始盘条加热工艺即钢坯在加热过程中局部过热有关。
制备断口纵截面试样在显微镜下检验晶粒度,发现套圈外壁晶粒度明显比基体晶粒度要粗,形貌如图8所示。因此推测断口试样与原始盘条加热工艺即钢坯在加热过程中局部过热有关。

图八
2 缺陷盘条工艺追溯及套圈用轴承钢盘条生产工艺改进
通过对开裂样品进行低倍、硬度、碳化物、断口、晶粒度等进行检测,低倍组织、碳化物均匀性、表面硬度均正常,而断口存在过热组织,且套圈外壁晶粒度明显比基体晶粒度要粗,推测这与原始盘条加热工艺即钢坯在加热过程中局部过热有关。
对开裂批次盘条加热工艺进行追溯,轧制批号C60199901共47支坯料,在换轧该规格时已入炉,离炉头仅10个步距,预热段701~715℃,加热一段952~959℃,加热二段1148~1156℃,满足工艺要求,而均热段1245~1248℃,加热二段和均热段高温段时间126分钟,超出工艺规范上限。
为迅速解决轴承钢盘条冷镦套圈开裂现象,对轴承钢盘条加热工艺进行优化:
(1)对轴承钢坯料入炉位置进行优化。在换辊时用于做套圈的轴承钢坯料不允许直接进入加热一段,第1支坯料离炉头出钢位置至少48个步距,如图9所示。当过渡钢种不够时,需空出足够的步距,利用换辊时间按正常出钢节奏走完空的步距,以防止轴承钢坯料在炉内加热段长时间停留而产生局部过热缺陷。
通过对开裂样品进行低倍、硬度、碳化物、断口、晶粒度等进行检测,低倍组织、碳化物均匀性、表面硬度均正常,而断口存在过热组织,且套圈外壁晶粒度明显比基体晶粒度要粗,推测这与原始盘条加热工艺即钢坯在加热过程中局部过热有关。
对开裂批次盘条加热工艺进行追溯,轧制批号C60199901共47支坯料,在换轧该规格时已入炉,离炉头仅10个步距,预热段701~715℃,加热一段952~959℃,加热二段1148~1156℃,满足工艺要求,而均热段1245~1248℃,加热二段和均热段高温段时间126分钟,超出工艺规范上限。
为迅速解决轴承钢盘条冷镦套圈开裂现象,对轴承钢盘条加热工艺进行优化:
(1)对轴承钢坯料入炉位置进行优化。在换辊时用于做套圈的轴承钢坯料不允许直接进入加热一段,第1支坯料离炉头出钢位置至少48个步距,如图9所示。当过渡钢种不够时,需空出足够的步距,利用换辊时间按正常出钢节奏走完空的步距,以防止轴承钢坯料在炉内加热段长时间停留而产生局部过热缺陷。
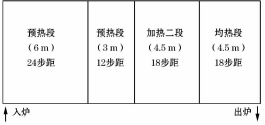
图九
(2)对轴承钢坯料加热时间进行优化,控制轴承钢坯料在进入加热二段和均热段后的高温段停留时间不超过100min。
(3)对轴承钢坯料加热温度和出钢温度进行优化,为避免轴承钢坯料在炉内高温段出现局部过热现象,严格控制加热温度,加热段和均热段的最高加热温度不超过1220℃,除鳞后红钢温度不超过1130℃。
3 工艺改进实施效果
工艺改进后再次生产供某用户生产18mm规格套圈用轴承钢盘条GCr15-Y,炉号16706548共45支坯料。换轧18mm规格时该炉号坯料只入炉24支,换辊时间为50min,换辊后生产过程比较顺利,加热二段和均热段的高温段停留时间为68min,加热二段温度为1135℃,均热段温度为1212℃,除鳞后红钢温度为1122℃。
取本批次盘条样品和以往产生过热缺陷的盘条做奥氏体晶粒度对比,发现存在过热缺陷的盘条边部晶粒度明显粗大,而本次盘条晶粒度比较均匀细小,如图10所示。
(3)对轴承钢坯料加热温度和出钢温度进行优化,为避免轴承钢坯料在炉内高温段出现局部过热现象,严格控制加热温度,加热段和均热段的最高加热温度不超过1220℃,除鳞后红钢温度不超过1130℃。
3 工艺改进实施效果
工艺改进后再次生产供某用户生产18mm规格套圈用轴承钢盘条GCr15-Y,炉号16706548共45支坯料。换轧18mm规格时该炉号坯料只入炉24支,换辊时间为50min,换辊后生产过程比较顺利,加热二段和均热段的高温段停留时间为68min,加热二段温度为1135℃,均热段温度为1212℃,除鳞后红钢温度为1122℃。
取本批次盘条样品和以往产生过热缺陷的盘条做奥氏体晶粒度对比,发现存在过热缺陷的盘条边部晶粒度明显粗大,而本次盘条晶粒度比较均匀细小,如图10所示。
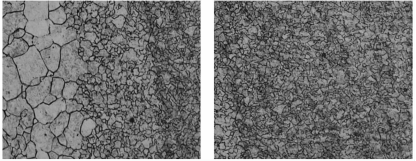
图十
用户使用该批盘条后未再投诉相关质量问题,据用户反馈冷镦套圈过程中开裂比例明显下降,从10%以上下降到0.5%以内。
4 结论
轴承钢盘条冷镦套圈开裂与原始盘条加热工艺即钢坯在加热过程中局部过热有关,在套圈用轴承钢盘条生产计划编排时应尽量避免轴承钢坯料在换辊时直接进入加热一段,实在无法避免时应按排过渡钢种或空出相应步距。
严格控制加热温度和加热时间,钢坯进入加热二段和均热段后的高温段停留时间不超过100min,最高加热温度不超过1220℃,除鳞后红钢温度不超过1130℃。
采用改进后的工艺连续生产多个批次,一直未出现批量开裂质量投诉。
4 结论
轴承钢盘条冷镦套圈开裂与原始盘条加热工艺即钢坯在加热过程中局部过热有关,在套圈用轴承钢盘条生产计划编排时应尽量避免轴承钢坯料在换辊时直接进入加热一段,实在无法避免时应按排过渡钢种或空出相应步距。
严格控制加热温度和加热时间,钢坯进入加热二段和均热段后的高温段停留时间不超过100min,最高加热温度不超过1220℃,除鳞后红钢温度不超过1130℃。
采用改进后的工艺连续生产多个批次,一直未出现批量开裂质量投诉。
来源:《金属材料与冶金工程》2016年05期